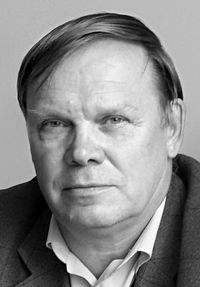
Валерий Воротников, доцент кафедры «Вагоны и вагонное хозяйство» МГУПСа, к. т. н.
Совершенствование технологических процессов ремонта узлов вагона позволит существенно повысить производительность труда на вагоноремонтных предприятиях.
– Валерий Геннадьевич, что такое производственный потенциал вагоноремонтных предприятий?
– Виды и объёмы работ для каждого отдельного вагона можно определить лишь в процессе ремонта, что сдерживает применение в ремонтных депо высокопроизводительной и соответственно дорогостоящей техники. В свою очередь это оборачивается определёнными противоречиями в сформированной производственной структуре вагонных депо, мощность и работа которых характеризуется совокупностью не взаимосвязанных показателей.
Это основные производственные фонды, средства и ресурсы производства, технологическая и нормативная документация. Они отражают не эффективность, а лишь состояние и использование имеющихся производственных ресурсов.
В условиях научно-технического прогресса в структуре вагоноремонтных предприятий необходимо формировать производственный потенциал. Он подразумевает возможность ремонта подвижного состава различного типа и новых конструкций вагонов, способность к стабильному функционированию системы планирования, управления, ценообразования и других, оперативное реагирование на изменение конструкторско-технологических характеристик вагонов, эффективное применение новой техники в условиях непостоянства объёмов работ при ремонте вагонов.
– Как оценить эффективность использования производственных ресурсов?
– Одним из ключевых моментов является уровень механизации технологических процессов ремонта узлов вагона, в котором учитываются трудозатраты рабочих на выполнение технологических и транспортных операций. Сегодня диапазон механизации для вагоносборочных участков составляет от 12 до 55%, для тележечных – от 20 до 60%, для колёсно-токарных – от 36 до 78% и для контрольных пунктов автосцепки – от 26 до 84%.
По нашим расчётам, при совершенствовании организации технологических процессов ремонта производительность труда в вагоносборочных участках можно повысить до 82%, в тележечных – до 70%, в колёсно-токарных – до 80% и в контрольных пунктах автосцепки – от 78%. Соответственно это обеспечит значительное увеличение в них эффективности использования технических, трудовых, энергетических и других ресурсов.
– Почему не нашёл широкого применения поточный метод ремонта вагонов?
– В настоящее время сформированная в вагонных депо организация технологических процессов предусматривает выполнение транспортных операций самими ремонтниками. При этом они используют универсальное подъёмно-транспортное оборудование – мостовой кран, кран-балка и т.п. Это соответствует условиям ремонта вагонов стационарным методом. На протяжении многих лет выполнялись научно-исследовательские работы по технико-экономическому обоснованию применения в вагонных депо поточного метода ремонта вагонов с использованием конвейерных линий с жёстким циклом функционирования. Технические возможности таких конвейеров могут быть реализованы только при неизменном перечне и объёме выполняемых работ при серийном изготовлении новой продукции. Кроме того, не уделялось должного внимания разработке эффективных конструкций конвейеров, обеспечивающих применение поточного метода ремонта.
Вместе с тем специалистами кафедры разработана концепция поточного метода ремонта узлов вагона с применением конвейеров модульного типа с гибким циклом функционирования. Их конструкция имеет ряд новых технических решений. Они могут быть применены в вагоносборочном, тележечном, колёсно-роликовом производственных участках и в контрольных пунктах автосцепки депо.
Такое оборудование позволяет изменять направление перемещения как самих вагонов, так и отдельных его узлов в процессе ремонта и обеспечивает повышение непрерывности и ритмичности выполнения технологических процессов. При этом время нахождения каждого отдельного вагона в ремонте зависит от фактического его состояния.
Модульными конвейерами с гибким циклом можно управлять в автоматическом режиме. В результате они позволяют исключить труд рабочих при выполнении транспортных операций. Применение гибких производственных систем обеспечит повышение мощности производственного потенциала вагоноремонтных предприятий, качества и эффективности ремонта вагонов.
Разработаны и другие конструкции новой техники для ремонта подвижного состава, не имеющие аналогов в России. На них получены патенты и авторские свидетельства. Это модули поворотно-транспортных систем для перемещения узлов вагона в процессе ремонта, подъёмно-транспортные агрегаты для подъёмки и перемещения кузова вагона по всему периметру вагоносборочного участка депо, манипулятор для разборки и сборки рессорного комплекта тележек грузовых вагонов, очистительно-нагревательный комплекс с гидростатической системой очистки моющих растворов, используемых при обмывке деталей и узлов вагона. В нём применены экологически чистые технологии.
Конструктивные схемы и принцип действия разработанной техники были представлены на прошедшей недавно II конференции ОАО «РЖД» «Повышение автоматизации и механизации при ремонте подвижного состава на железнодорожном транспорте».
– Какие ещё разработки ведутся в области совершенствования вагоноремонтного производства?
– Профессором Михаилом Болотиным разработана концепция взаимосвязанного оптимального повышения технического уровня производства вагонных депо и конструкций вагонов. Впервые создана математическая модель депо как системы автоматического регулирования производительности, которая позволяет выбирать такие параметры производственных процессов и технологических машин, которые обеспечивали бы его устойчивую работу при условии спада или роста объёмов ремонта и т. д.
Разработана теория экспертизы качества ремонта вагонов в депо, учитывающая применяемую технологию, уровень повреждаемости вагонов и технического производства, степень соблюдения правил ремонта.
Беседовал Роман Мартынов
Справка «Гудка»
В ходе II конференции ОАО «РЖД» «Повышение автоматизации и механизации ремонта подвижного состава на железнодорожном транспорте» в июне в Щербинке учёные и специалисты в области ремонта подвижного состава со всех железных дорог страны постановили, что обеспечить современные условия работы ремонтных предприятий компании возможно лишь за счёт разработки и внедрения инновационных решений в области автоматизации и комплексной механизации ремонтного процесса, использования новых материалов, систем диагностики и управления.